Insert Moulding
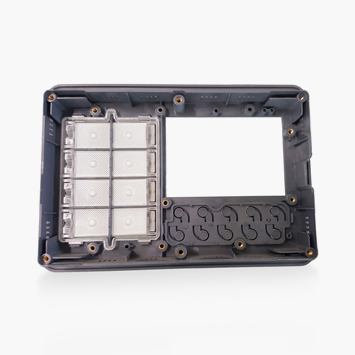
Insert Moulding combines metals and plastics or multiple combinations of materials and components into a single unit
The process ensures plastics have an improved tensile strength and wear resistance
Insert moulding reduces assembly and labour costs, reduces the size and weight of the part, improves component reliability, and delivers improved part strength and structure with enhanced design flexibility
Solid pellets of raw material are melted and extruded into a mould. The metal or plastic insert is placed in the precision location in the mould by the operator before starting the process - the plastic melt solidifies over the inserts and becomes one inseparable part - and then the press opens and the moulded parts are ejected.
Insert moulding uses the same materials as the injection moulding process. For extreme high heat - engineered thermoplastics are used. These materials withstand very high temperatures and the components can withstand a very harsh environment because of the physical, electrical and chemical properties.
We have approved vendors for supplying brass, stainless steel and mild steel inserts with or without plating with high standards of precision, consistency, reliability and on-time delivery. This helps us to mould large volumes of insert moulded parts with almost no damage to the moulds